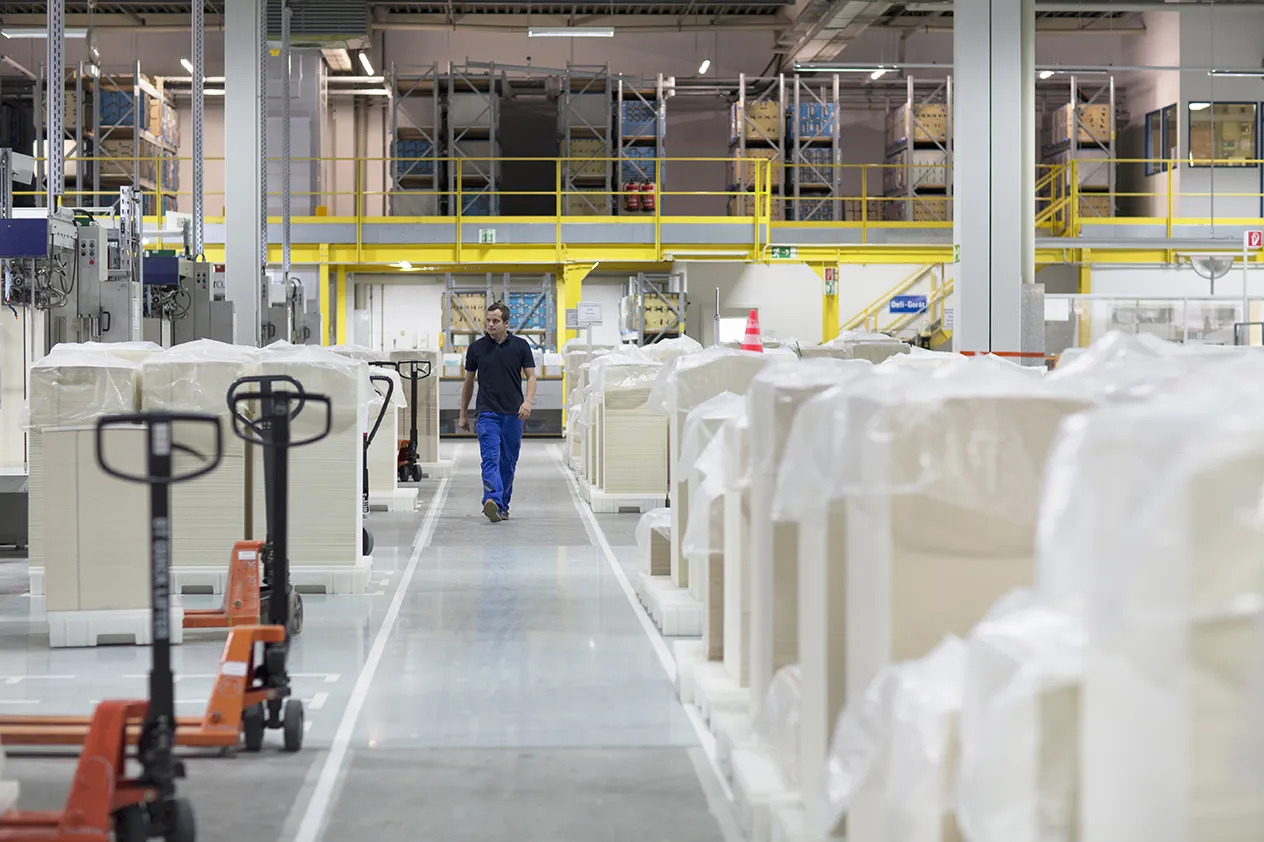
In the past few years, e-commerce has grown by leaps and bounds, and so has the need for packaged food. This increased the amount of pallet stretch film-based packing.
As pallet wrapping is a cost-effective and efficient way to package pallets for storage, shipping, and distribution, most of the manufacturing units have mechanized their stretch wrapping techniques.
Automation of all industrial processes in the packaging industry has also set the stage for pallet wrapping machines. This highly stretchy plastic film keeps items tightly together and keeps them waterproof once packaged with one another, making them perfect for travel or storage.
The rise of the transportation and logistics industry with warehouses is driving market growth and has resulted in the packaging of both durable and non-durable goods with pallet wrap. The pallet stretch film comes in different grades, widths, and colors for different applications.
However, proper pallet wrapping techniques have common procedures. Within the available options for wrapping, stretch film reels are among the most sought after packing materials and are considered to be an effective way to package products.
Best Tips for Pallet Wrapping Techniques
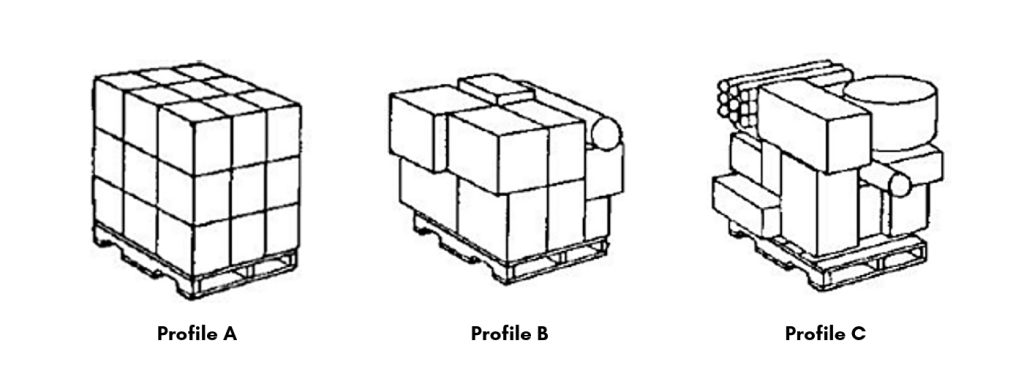
1. Pallet Load Configurations
There are three basic load configurations of A Profile load, B Profile load, and C Profile load. So choosing the right pallet and the right load should be of the utmost importance.
A-profile load
The most common loading profile is stacked evenly from the bottom to the upper part of the pallet. The load footprint of profile A is the same size as the blade shape, and the product stacks have a uniform shape with no irregularities or protrusions.
These are the easiest load profiles to attach using a stretch film.
B-profile load
This pallet loading configuration is smaller than the dimensions of the pallet or from the base of the pallet. Profile B loads are also uneven in shape and range from wide to narrow when extended upwards.
Stretch wrappers find Profile B loads difficult to fix due to inconsistency in surface alignment.
C-profile load
In this the lower layer is larger than the pallet dimensions and is just opposite of B-Profile load.
2. Equipment
A manual wrap dispenser could be used, but it would be very difficult to wrap a large quantity. A pallet wrapping machine with the proper degree of automation would be much more convenient.
3. Securing the Film
The pallet wrapping begins at the bottom and spirals upward toward the top. To fix the leading end of the stretch film to the pallet base, most technicians begin by twisting it. Not tying a knot also saves time for whoever unpacks the loaded pallet.
4. Wrapping the Product
An experienced operator would give two or more circles around the base and provide 360-degree wrap protection so there is a grip anchoring the load to the pallet stretch.
Automated stretch wrappers can have specific overlap coverage depending on the material used for the job.
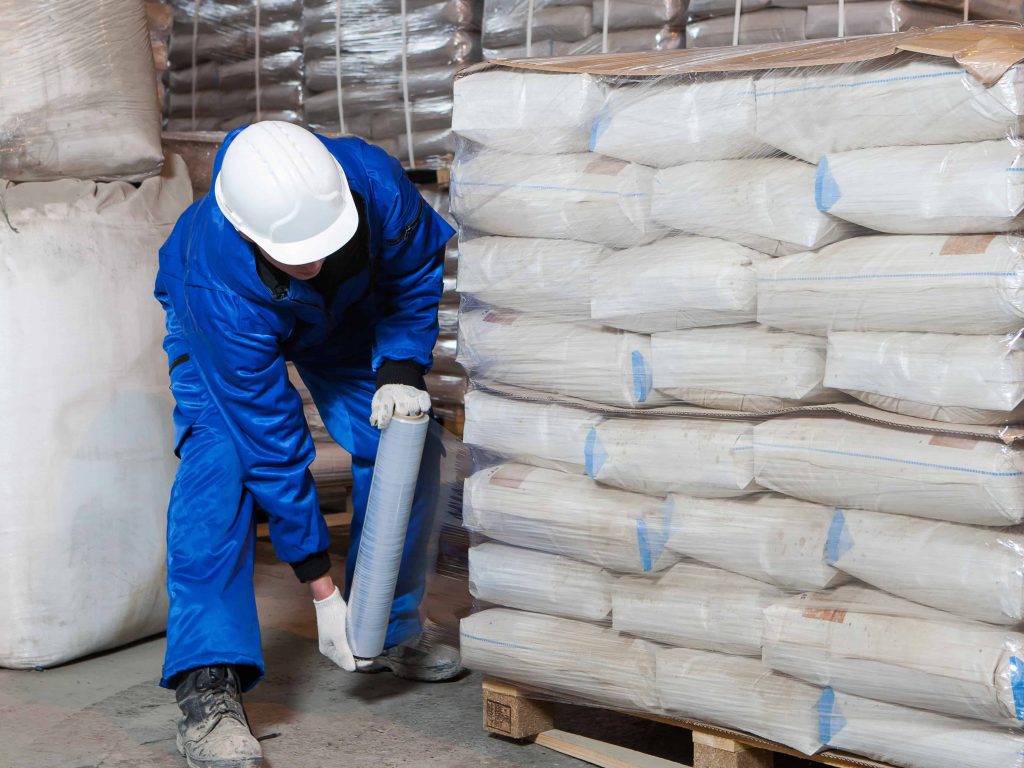
5. Control Wrap Tension
This is one of the important pallet wrapping techniques as tension helps in controlling the tightness and compression of the load. This varies according to a crushing factor where sensitive products require a slight strain compared to the envelope stretching factor.
Heavy and strong loads withstand greater tension, and this is a key element to ensuring that the load is packed as firmly as possible. It is difficult to apply the same tensile force when packing by hand.
On the other hand, stretching machines have an even strength due to their predefined instructions.
6. Decide Upon Double Wrapping
Stretch wrap operators have a choice to make when they reach the top of their upward spiral. They can either tie-off the wrap on top of the load or reverse course and spiral downhill.
As a matter of abundant precaution, always double wrap when in doubt, as this safety measure is a security measure for stretch wrap film and can prevent it from getting damaged easily. This can be an individual decision, depending on the load being wrapped.
7. Tie off the Wrap
The worker completing the packing may choose whether to attach the stretch film to the end or above the load. This step is needed to execute an appropriate pallet packing technique. It can attach to the end of the package for top or bottom charging.
All in All
Appropriate stacking options with different combinations of stack design must be taken into consideration when packing and stacking boxes. Properly packed pallets ensure product safety and smooth travel with minimum transit loss.